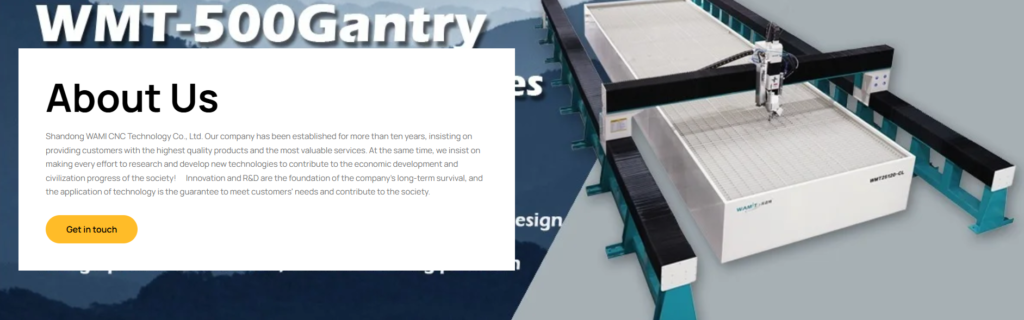
Water jet cutting is a highly versatile and precise manufacturing process used across various industries, from aerospace to automotive. It utilizes high-pressure water, sometimes mixed with abrasive materials, to cut through different materials, including metal, glass, stone, and composites. This guide explores how water jet cutting works, its advantages, and its applications in modern industries.
How Water Jet Cutting Works
Water jet cutting technology operates by directing a high-pressure stream of water or a mixture of water and abrasive particles at a material to cut through it. The process involves:
- High-Pressure Pump: Water is pressurized up to 60,000 PSI or more.
- Mixing Chamber: If required, abrasive particles (like garnet) are added to enhance cutting ability.
- Cutting Nozzle: A precisely focused jet stream exits through a small nozzle to cut materials with extreme accuracy.
Advantages of Water Jet Cutting
- Precision Cutting: Can achieve tolerances as tight as +/- 0.1mm, making it ideal for intricate designs.
- No Heat-Affected Zones (HAZ): Unlike laser or plasma cutting, water jet cutting does not generate heat, reducing the risk of material warping.
- Versatile Material Cutting: Can cut metal, glass, ceramics, composites, and even food products.
- Eco-Friendly: Uses water and natural abrasives, making it more environmentally friendly than other cutting methods.
- Minimal Waste: Reduces material wastage, saving costs and resources.
Applications of Water Jet Cutting
Water jet cutting is used in multiple industries, including:
- Aerospace: Cutting titanium, aluminum, and composite materials for aircraft parts.
- Automotive: Fabrication of gaskets, metal panels, and customized components.
- Architecture & Construction: Intricate stone, tile, and glass designs for aesthetic purposes.
- Manufacturing: Creating machine parts with high precision and minimal material loss.
Water Jet Cutting vs. Laser Cutting
Water jet cutting and laser cutting are often compared due to their precision and industrial applications. Here’s a quick comparison:
Feature | Water Jet Cutting | Laser Cutting |
---|---|---|
Heat Impact | None | Creates HAZ |
Material Versatility | High | Limited to certain materials |
Cutting Thickness | Up to 12 inches | Generally up to 1 inch |
Eco-Friendliness | Uses water and abrasives | Emits gases and requires energy |
For a deeper dive into the Water Jet Cutting vs. Laser Cutting comparison, check out our detailed guide.
To explore more about industrial cutting technologies, visit:
Conclusion
Water jet cutting is a powerful and versatile technology that offers precision, efficiency, and eco-friendly advantages over traditional cutting methods. Whether for aerospace, automotive, or artistic applications, it remains a top choice for businesses looking for high-quality cutting solutions.
For more insights into advanced manufacturing technologies, stay tuned to our blog!